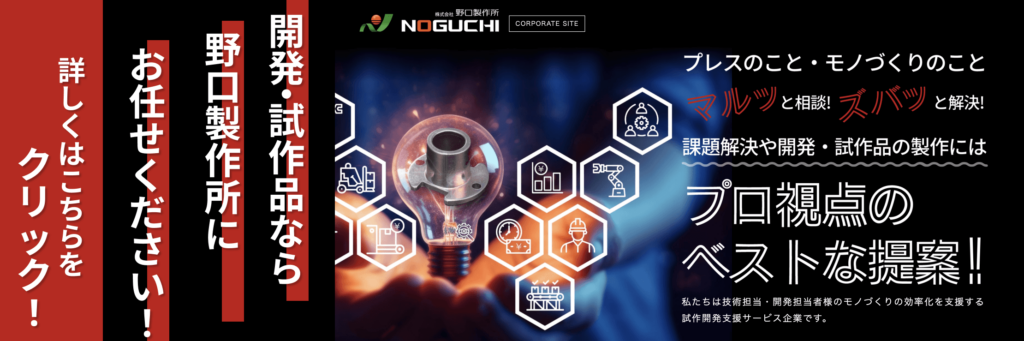
プレスやモノづくりの課題を解決!開発や試作品制作に関する内容はこちらをご確認ください!
Contents
絞り加工とは
絞り加工とは、板金加工の一つで1枚の金属板(平板)に圧力を加えることで円筒・角筒・円錐などの容器形状(凹形状)にする加工方法の一つです。
用途が非常に多い絞り加工形状は、私達生活の身近なところでたくさん使われており、例えばアルミ缶・フライパン・灰皿などがイメージし易いかと思います。
また、繋ぎ目の無い形状が一番の特徴であり、多種多様な形状加工ができることから、生活の身近な物から工業製品・機械部品等の目に見えないところにも、数多く利用されています。
絞り加工はプレス加工の工法の中でもっとも技術の経験が必要な工法であり、金型設計が難しいと言われています。
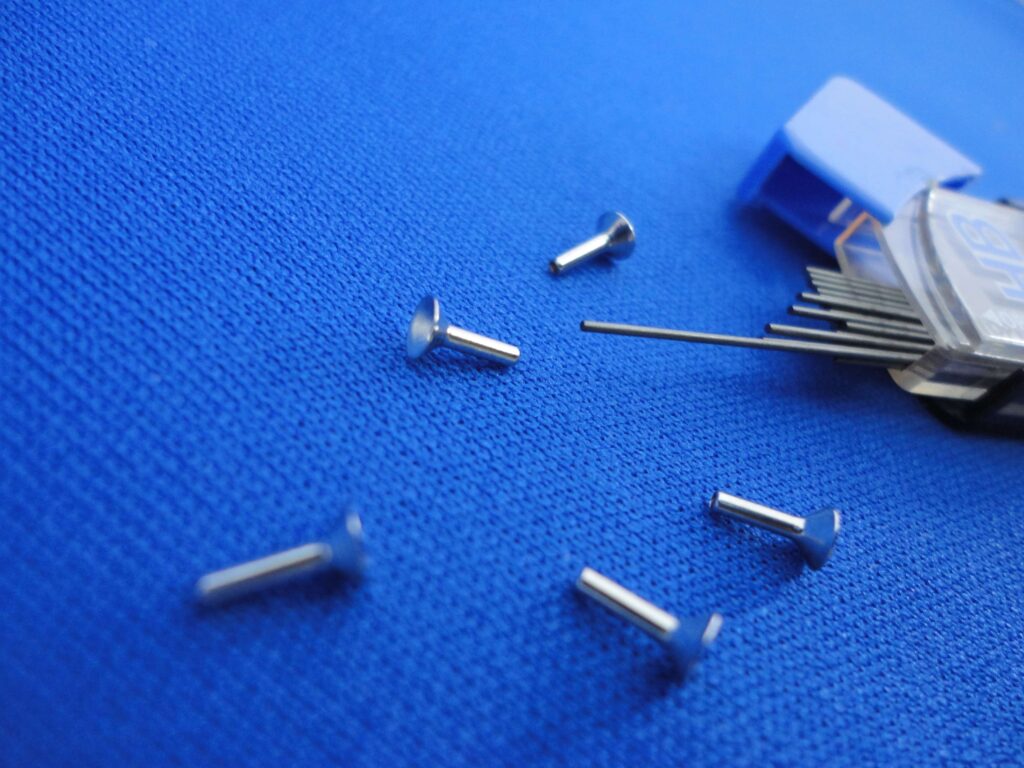
絞り加工の種類
絞り加工は、絞るカタチによって3種類に分けられます。
- 円筒絞り
- 角筒絞り
- 異形状絞り
円筒絞り
板材を円筒形状に塑性変形させる加工です。
もっとも基本的な絞り加工です。
角筒絞り
板材を四角形状に塑性変形させる加工です。
製品はシンクや弁当箱のような形になります。
異形状絞り
板材を自動車のパネルなどに使われるような複雑な形状に塑性変形させる加工です。
深絞り?浅絞り?
絞りの深さによる分類で、製品の直径に対して製品の深さが長いものを深絞り、短いものを浅絞りと言います。しかし、定義はあいまいで同じ深絞りでも直径に対して長さが2倍のものもあれば、5倍、8倍、10倍のものもあります。これは全て深絞りに分類されます。
金型構成と仕組み
次に、絞り部品を加工するための金型構成と仕組みについてです。
加工に使用される金型は大きく分けて『パンチ(雄型』・『ダイ(雌型』・『ブランクホルダ(シワ押さえ板)』の3つで構成されています。
絞り加工の仕組みについては、製品形状になる下型の金型『ダイ』と、圧力を加える上型の金型『パンチ』がペアになっていて、一枚の板に圧力を加えることで求める形状に加工していきます。
まず、シワ押さえ板である『ブランクホルダ』と『ダイ』の間に板材を挟み込み、押し付けた後、『パンチ』が降下しシワ押さえ板に圧力をかけます。そして、その『パンチ』の下端部の形状に沿って板が変形し『ダイ』の空間内部に押し込まれていきます。更に『パンチ』の降下が進むと『ブランクホルダ』で抑えられていた周辺部が『ダイ』の中へ引き込まれていき、成形が行われます。
その一連の加工において、形状・設備・成形条件を考慮し適正に加工しないとシワ・ヒズミ・割れなどが発生してしまい不良の原因になってしまうため、1回に絞れる経・深さの限界・シワの発生を抑える設定を設計段階で把握しておかなければなりません。
そのため、希望の形状になるまで複数回繰り返すものもありますが、繰り返しの加工において、材料は加工硬化して絞りづらくなることも併せて覚えておく必要があります。
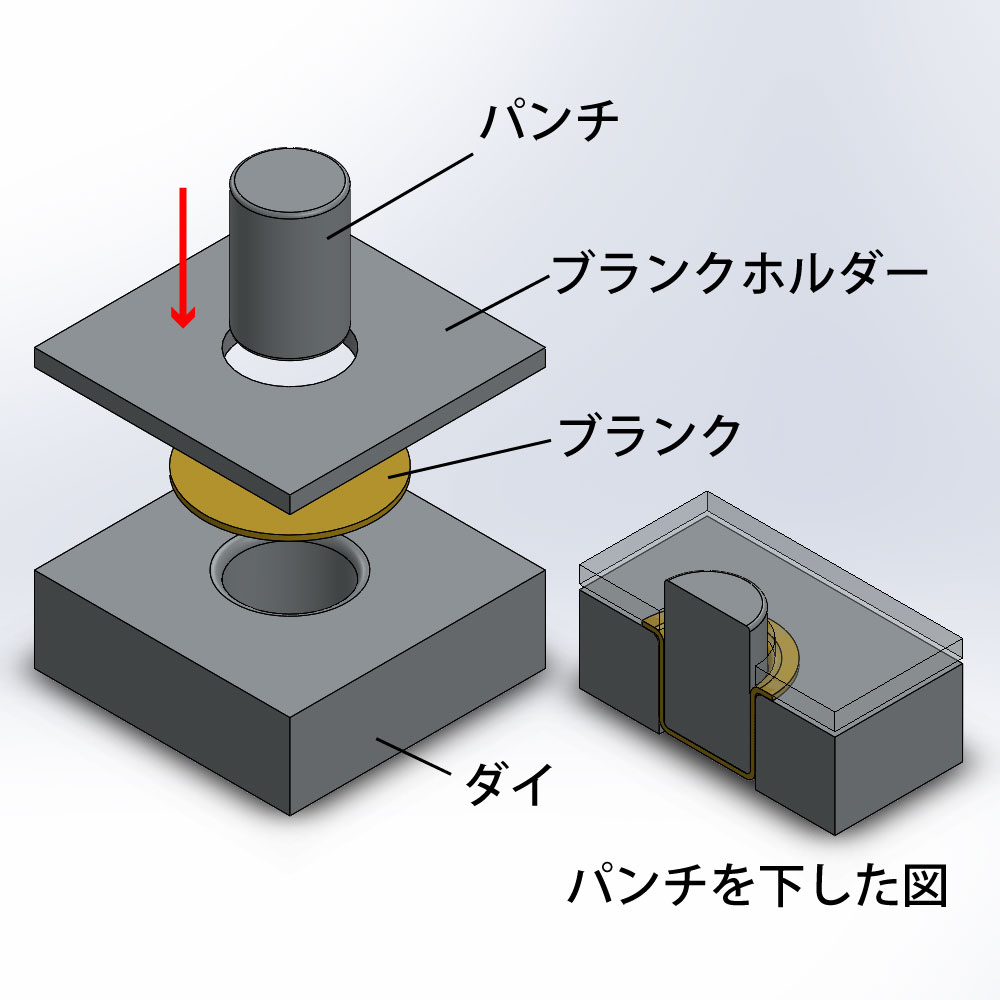
https://mono-mado.com/dictionary/drawing
工程設計
基本的な工程設計は以下の通りです。
①ブランク形状と寸法決め
ブランクとは素材の板を指します。
まずはブランクを絞り加工して形状を変えていくのですが、1回に絞れる径には限界があり、最初の絞り工程「初絞り」の後に、「再絞り」を繰り返して加工することを念頭に置いた設計を行います。
ブランクの直径は、フランジと絞り部分の直径、さらに絞り部分の高さの3つです。
ブランクの直径は以下の式によって表されます。
D=√d^2+4dh)
D:ブランク直径 d:絞り部直径 h:絞り部高さ
②絞り工程数決め
絞り率を基準に1回あたりの絞り径を計算して、絞り回数を決めます。
③金型設計
パンチとダイ2種類を合わせた金型の設計を行っていきます。
ダイの設計はパンチがダイの中に入り込んだ時のクリアランスを基準に直径を計算します。
またパンチの設計は、パンチの直径と肩半径の計算が必要です。
④プレス機械決め
工程設計で計算された絞り加工力を基準に、トルク出力を満たすものを選定します。
絞り加工力は、以下の式の計算で出します。
絞り加工力(P)=K・n・d・t・Ts(kgf)
K:係数 n:円周率 d:絞り径 t:板厚 Ts:引っ張り強さ
⑤油の選定
潤滑油には油性タイプと水性タイプの2種類があります。
油性タイプ
メリット:汎用性が高く、安価。防錆性を付与できる。
デメリット:温度の影響をうけやすく熱がこもりやすい。油なので作業環境を汚してしまう。
水性タイプ
メリット:冷却性が高く、摩擦熱を冷却可能なので高速生産に向く。
デメリット:錆のリスクがある。
もちろん被加工材の材質、加工性などの加工条件に応じた潤滑油の選定が必要です。
野口製作所では、難加工材と言われているステンレス・アルミ・銅等の非鉄材の抜き加工・曲げ加工はもちろんのこと、特に深絞り加工を得意としております。
各種業界(家電・車載・医療・センサー等)向けの絞り加工実績があり、お客様の困り事・課題を弊社技術でご提案させていただきます。
プレス加工へのこだわり
良い品質のプレス加工製品は良い金型から生まれます。私たちは金型の設計・製造にこだわりを持って臨んでいます。野口製作所のこだわりはこちら
野口製作所からのメッセージ
野口製作所は昭和 42 年の設立以来、金属プレス加工を通して御客様の課題を解決す る提案型企業として成⻑して参りました。
私たちのコア技術はプレス加工の工法の一つ、深絞り加工です。
この深絞り加工技術で 製作した製品を電子機器部品、車載部品で使って頂いています。
また、医療機器として 製作している製品の中には、これまで実現できなかった非常に微細で薄肉の製品を深絞 り加工技術により製作に成功したものもあり、お客様の事業拡大に大きく貢献しまし た。
このように私たちは幅広い市場ニーズにお応えする製品製作をしております。どんな時でも私たちが大切にしているのは、御客様の課題に共に悩み、解決のための最 適解を提案するきめ細かい伴奏型のものづくりサービスです。
御客様の伴走者として共に成⻑していくことは最大の喜びだと考えています。 そのためにも、まずは社員一人ひとりが人間力を鍛え、正しい判断で御客様へ寄り添える人 財の育成が何よりも大切だと感じ、日夜人財育成に努めております。
これからも私たちは、世界中のお客様の期待をこえる価値を、安心というカタチで提供し ていきます。
弊社の詳細な情報につきましては、下記のリンクから資料をダウンロードしてご確認ください。
またお困りごとや相談したい内容がございましたら、HP の画面最下部の「お問い合わせ」からご相談ください。
皆様からのご連絡をお待ちしております!
野口製作所のこだわりのダウンロード資料はこちら
お問い合わせはこちら
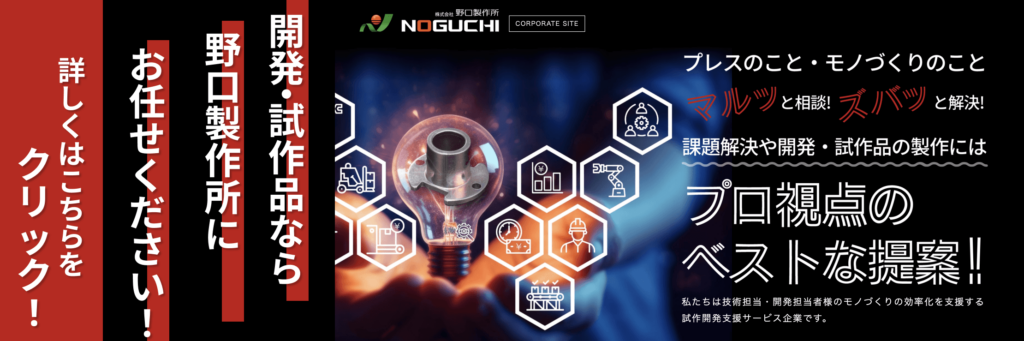
プレスやモノづくりの課題を解決!開発や試作品制作に関する内容はこちらをご確認ください!